What is the Difference Between Vapor Compression vs. Multiple Effect Distillation
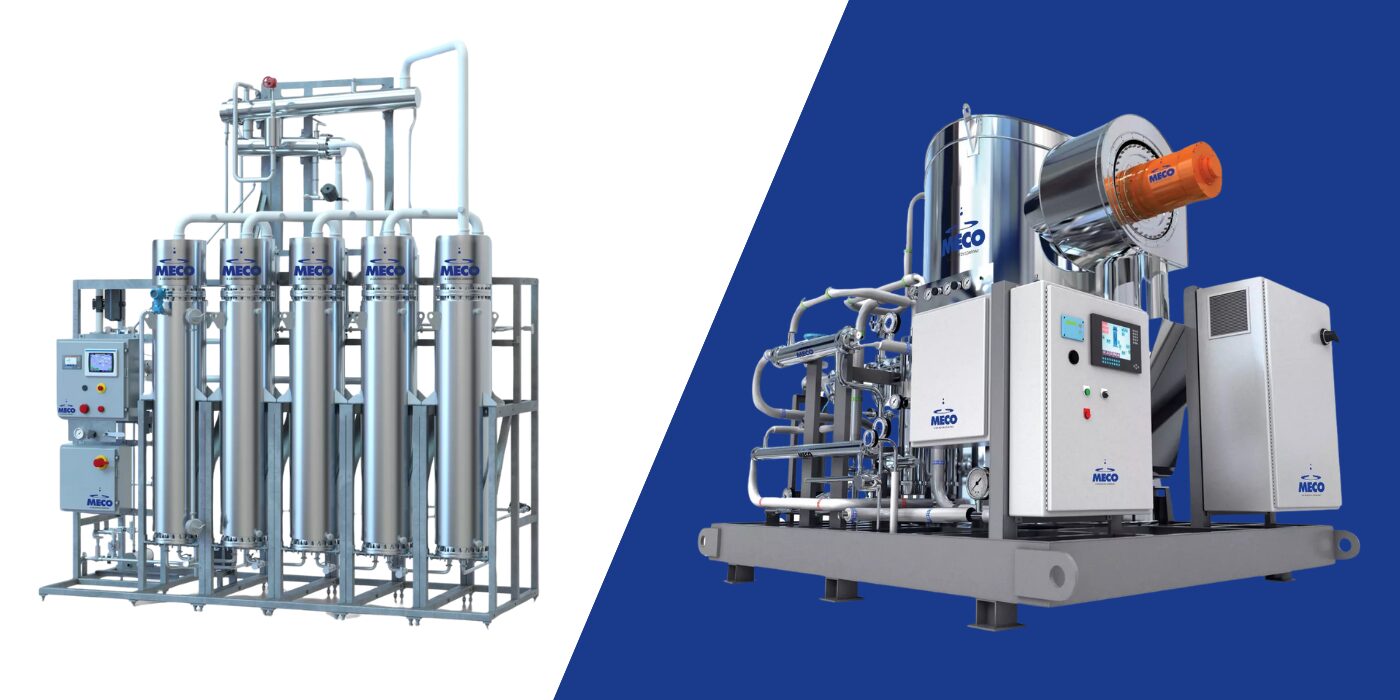
Water for injection (WFI) is vital for parenteral drug administration, as this extremely high-purity water permits the dilution of pharmaceutical substances for injection or intravenous application. Creating the purest water possible for this purpose can be accomplished using two common methodologies — vapor compression (VC) and multiple effect distillation (MED).
Before water undergoes one of these processes, it must pass through a series of initial purification measures potentially including dichlorination, softening, deionization, UV disinfection, or reverse osmosis. Only then is it ready for VC or MED processing to take it to the purity level required for use as Water for Injection?
Comparing Vapor Compression versus Multiple Effect Distillation requires an understanding of the two processes and how they differ in their approaches.
What is the Vapor Compression Distillation Cycle and How Does it Work
Originally designed for desalination purposes, the Vapor Compression (VC) concept is a distillation process consisting of a single evaporator where feed water boils, converting to steam, which is then condensed to form Water for Injection (WFI). The steam undergoes a preheating and decarbonization initial heating cycle before entering a compressor, that removes CO2, oxygen, and other dissolved gases from the feed water before entering the steam evaporator, helping reduce corrosion and lower conductivity in the final WFI product. This system raises the steam’s pressure to about 3 ½ psi, directing it to the outside of the tubes in the evaporator. The thermal economy or efficiency of the VC process results from recycling latent heat, eliminating the need for a separate condenser that uses cooling water.
When the water becomes steam, it is captured by tubes and brought to a demister to remove solid entrained droplets. The remaining pure vapor condensate accumulates on the evaporator tubes’ exterior as distillate, then collects at the bottom of the tube sheet and is withdrawn by a distillate pump, discharging it through one or more shell-and-tube heat exchangers. In VC systems, feed water is preheated through heat exchangers and introduced into the steam evaporator to boil at approximately 1 psi.
From there, a distillation pump passes it through a cooler, after which it becomes WFI. Vapor compression distillation can produce WFI at both hot and ambient temperatures without needing cooling water by adding a few extra distillate coolers.
What Is Multi Effect Distillation?
The multiple effects that give the MED process its name arise from the process passing the water through several different “effects,” or cells, to accomplish the goal of purification, typically ranging from 3 to 8. Plant steam is fed to the first effect to heat the water and create Pure Steam. Each effect is a pressure vessel that resembles a shell and tube heat exchanger, with an extended head for steam disengagement. The process involves natural circulation, or rising film design, where feedwater flows up through the tubes, and plant steam is introduced on the shell side.
The first effect operates at pressures of 60-80 psi, with steam condensing on the tubes’ outside, transferring heat to the water inside to produce more Pure Steam. Steam from the last effect is directed to a feedwater condenser, using feedwater to condense, cool, and heat it. MED systems require separate condensers using cooling water, where Pure Steam from the last effect is condensed and any leftover steam is sub-cooled to the designed temperature.
MED operates at higher temperatures and pressures than VC systems, necessitating better feedwater quality. Each effect contributes to a portion of the total WFI output, ensuring the water meets quality requirements while minimizing scale formation through a blow-down process. The remaining vapor is exposed to the coolest temperature yet, causing it to condense on the heat exchanger and become distillate. This distillate, now WFI, is then extracted via a pump.
The Advantages of Vapor Compression and Multiple Effect Distillation
Though both are effective purification systems utilizing similar principles, MED and VC have numerous distinct advantages. While multiple effect distillation has long been the most common method used for water purification, vapor compression has gained traction as an alternative due to some of its attractive benefits.
Both systems produce Purified Water and the more stringently regulated Water for Injection (WFI), ensuring 100% microbial kill by operating at self-sanitizing temperatures. They can each meet pharmacopeial monographs with proper pretreatment. VC is uniquely capable of producing ambient WFI without cooling water, while MED can provide Pure Steam for headers. Which is best for a given application will depend on the required volume of water and the nature of the operation.
The Benefits of Vapor Compression
Any distillation process will require some measure of feedwater pretreatment. However, Vapor Compression systems operate at a lower temperature than Multi Effect systems, giving them a greater tolerance to the presence of chloride and silica, components that can cause buildup and corrosion when exposed to extreme heat. They can therefore accept feedwater after a softening treatment, while MED equipment requires it to undergo reverse osmosis and dechlorination first.
The benefits of Vapor Compression (VC) include lower plant steam and cooling water requirements due to its thermal efficiency, as the process recycles latent heat, reducing the need for a separate condenser. VC systems can produce both hot and ambient WFI without the need for cooling water, allowing production at approximately 25 degrees above the incoming feedwater temperature by adding a few extra distillate coolers. This flexibility enables VC stills to cater to various temperature requirements in WFI production.
Of the two, vapor compression systems are more efficient in general. They continuously reuse the heat they generate, and the purified entrained droplets removed prior to distillation simply return to the feedwater to be processed again. This leads to generally reduced operating costs due to their thermal efficiency and minimal pretreatment requirements. The ability to use softened, dechlorinated water directly, without extensive pretreatment, further highlights the cost-effectiveness of VC systems. Vapor compression also yields the advantage of producing both hot and ambient WFI due to its processing methods.
Furthermore, VC systems tend to have a smaller footprint compared to Multiple Effect Distillation systems, potentially saving substantial space and associated real estate costs in a facility.
MECO’s GII Compressor
The compressor MECO designed and manufactures in house for our VC still is called GII Centurbo™ Compressor. It is a direct drive compressor with the impeller attached directly to the motor shaft eliminating the need for flex couplings, sheaves and gear boxes. The GII Centurbo™ Compressor is mounted directly on the steam evaporator, which eliminates the work of maintaining the ducting.
There are several benefits of our patented GII Centurbo™ Compressor. The compact design means it can be installed within 1-2 hours and is easier to access for maintenance. The impeller and suction bell are cast of Inconel and 316 stainless steel, and then machined to yield a smooth and homogenous surface finish less than 25Ra.The GII Centurbo™ Compressor has less than 10% of the parts of other industrial compressors for VC stills.
For a typical GII compressor, reducing the compressor speed by 25% will reduce the electrical consumption by 50%. Furthermore, reducing the compressor speed by 50%, will reduce the electrical consumption by 80%. Note that compressor speed is linked directly and proportionally to distillate production. So a MECO VC can produce half the named-plated flowrate, and a fifth of the electrical consumption. This is because we’re using a VFD (Variable Frequency Drive, sometimes known as Variable Speed Drive (VSD), to utilize the power law and run the compressor efficiently.
Perhaps most important is the GII compressor’s impact on vapor energy consumption. The GII technology enables a variable output of your distiller within a given maximum capacity. Instead of starting and stopping to produce a fixed output, MECO GII vaper compression water distillers have a variable output to meet diminished or increasing needs for production. As you can see from the chart, a 25% reduction in production capacity translates to a 40% reduction in compressor power.
Running at turndown can not only save money, but if the site has the WFI tank capacity and a flexible production consumption, running at lower flowrates keeps systems running and hot for longer, which has mechanical benefits (reduces the starts & stops which reduces wear and tear), and reduces risk to product quality because the system is kept in highly sanitary conditions for longer.
Learn more about our advances in Vapor Compression technology here.
The Benefits of Multiple Effect Distillation
Multiple Effect Distillation (MED) is particularly suitable for smaller WFI systems, as it enables simultaneous production of WFI and Pure Steam using plant steam. This dual capability can be beneficial for facilities that require both Pure Steam and WFI at any given time.
Though it may not be quite as efficient as a VC system in some ways, MED equipment comes with its own benefits. It still has a number of moving parts, but MED actually uses less electrical power by virtue of not having a compressor drive. Additionally, the somewhat modular nature of the multiple-effect design allows plants to choose the size of the system based on their requirements, with smaller units like three-effect systems representing a significantly lower upfront investment.
One unique benefit of multiple effect distillation is the ability to tap the first effect for purified steam. Some MED designs from MECO capitalize on this capability and will allow the user to produce WFI and Pure Steam simultaneously. Some even permit the release of purified steam from multiple effects. MED systems ensure robust water quality, while their multiple evaporator effects enhance efficiency by reducing utility consumption as more effects are added.
Although MED systems require separate condensers with cooling water for effective condensation and sub-cooling, they demand less electrical power and have lower maintenance needs due to fewer moving parts. While their gravity-based feed system may demand more headroom, these features make MED an effective choice for facilities with specific steam generation and quality assurance requirements.
Comparing VC vs. MED for Operational Needs
When comparing Vapor Compression and Multiple Effect Distillation for operational needs, several factors come into play, including feedwater quality, capacity requirements, utility costs, and infrastructure. In general, VC systems will cost more upfront but deliver lower operating costs, particularly when used to produce cold WFI. However, the disparity lessens significantly when comparing MED units with a higher number of effects and greater output demands.
For a facility that needs little Purified Water output and prioritizes floor space, the increase in cost per gallon of WFI may be worthwhile for a MED system that better fits its operational requirements.
Another important point when weighing VC versus MED is the quality and composition of feedwater available, as this will have a significant impact on the pretreatment demands for each system. VC systems, which are more economical for medium to large capacity operations, require less pretreatment and have a smaller footprint, saving space and costs. In contrast, MED systems are ideal for smaller WFI needs, offering simultaneous WFI and Pure Steam production. The choice between VC and MED should consider factors such as feedwater quality, system capacity, utility costs, and infrastructure availability.
Operating costs, including capital, utility, and maintenance expenses, are also crucial factors to consider. Ultimately, both technologies meet WFI quality requirements, and the decision should be based on an analysis of the total cost of ownership and site-specific constraints.
Pretreatment Requirements and Considerations
Effective pretreatment is essential for both Vapor Compression (VC) and Multiple Effect Distillation (MED) systems to ensure high-quality Water for Injection (WFI) production. VC systems benefit from a simpler and more cost-effective pretreatment process, as they can often use softened, dechlorinated water without the need for reverse osmosis (RO), owing to no feedwater Total Dissolved Solids (TDS) limit.
On the other hand, MED systems operate at higher temperatures and typically require single-pass RO to meet conductivity limits and manage hardness and silica levels effectively. The pretreatment process for both systems generally includes multimedia filters, softeners for hardness removal, and carbon filters for chlorine and chloramine elimination.
Maintaining proper feedwater quality is crucial to minimize scale formation within the stills; hardness scale is usually removed chemically, while silica scale may require mechanical removal. Setting appropriate blowdown rates based on pretreatment quality is vital for efficient operation and scaling prevention. To accommodate seasonal variations and maintain optimal performance, regular feedwater quality analyses are highly recommended.
Cost Analysis and Economic Considerations
When choosing between Vapor Compression (VC) and Multiple Effect Distillation (MED) systems, a thorough cost analysis is essential, encompassing both capital and operating expenses. VC systems are generally more efficient and cost-effective, particularly with softened feed water, due to their low plant steam and cooling water needs, which translate into reduced operating costs.
In contrast, while adding effects to a MED system can lower utility consumption, it does not increase WFI output, necessitating a detailed examination of utility costs and the total cost of ownership. The decision should account for site-specific factors such as utility costs, feedwater quality, and pretreatment needs.
Conducting detailed cost comparisons, including capital expenditures (CapEx) and operating expenses, is crucial to determining the payback period and economic viability of each technology. Ultimately, the choice should be based on a comprehensive evaluation of all associated costs, ensuring alignment with the facility’s operational and financial goals.
Footprint and Infrastructure Considerations
Footprint and infrastructure are critical factors when choosing between Vapor Compression (VC) and Multiple Effect Distillation (MED) systems. VC systems typically have a smaller footprint than MED systems, offering potential savings in space and real estate costs. For instance, a 20 GPM VC system is generally more compact than a MED system with up to 5 or 6 effects.
However, it’s important to consider the pretreatment infrastructure as well. MED systems often require extensive infrastructure, including reverse osmosis (RO) and electrodeionization (EDI) skids, along with softeners, multimedia filters, and carbon filters.
In contrast, VC systems, which can operate with softened water, usually need only multimedia filters, softeners, and a carbon filter, leading to a more streamlined setup. The decision should carefully consider available space, infrastructure capacity, and any modifications necessary to accommodate either system, ensuring they meet the facility’s spatial and operational needs effectively.
Contact MECO for Water Purification Processes and Solutions
MECO has over 95 years of experience delivering trusted water purification solutions, including innovative equipment for producing Purified Water, Pure Steam, and Water for Injection. MECO solutions produce over 25 million gallons of water a day for biotech and pharmaceutical organizations around the world.
Our worldwide reputation is fueled by our commitment to ensuring every operation can find the resources required to generate water with the appropriate purity level for its specific applications. The MECO team delivers expert product knowledge, industry experience, and an understanding of scientific principles to help clients select their ideal water purification solution.
For more on our vapor compression water distillers or multiple-effect distillation systems, connect with our team.