How to Produce Water for Injection With Vapor Compression Distillation
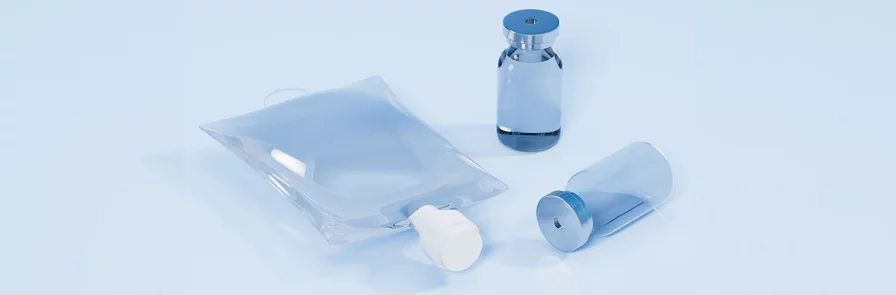
Water for Injection (WFI) is a critical element in the biopharmaceutical industry. Vapor compression distillation uses heat to evaporate water, producing WFI. Understanding vapor compression technology for WFI allows facilities to choose the most efficient and reliable equipment for the job.
This article delves into the use of Vapor Compression Distillers for producing Water for Injection. MECO’s innovative VC Still improves efficiency and reliability in creating high-quality WFI. Understanding the components of a water vapor compression distillation system, including our GII Centurbo™ Compressor, can assist you in making better decisions for your company regarding the best type of WFI generation system.
You can download a comprehensive cost review of four system designs for Water For Injection generation here.
Vapor Compression Distillation for WFI
During the vapor compression distillation method, a portion of the feedwater is evaporated, and the vapor is sent to the compressor. Here, mechanical energy is used to compress the vapor, which increases its pressure and temperature. The vapor is then condensed to form product water, called distillate. The released heat of the condensed vapor is recycled and used to evaporate the feedwater.
Water Vapor Compression Distillation System Components
The Vapor Compressor (VC) Still contains a single evaporator where the feedwater boils, converting the steam, and then where that steam — after it goes through the separator demister — condenses to form WFI. Other main components include:
- A direct drive
- Centrifugal compressor
- Decarbonator
- Heat exchangers, including the feed heater, blowdown cooler, distillate cooler, and distillate pump
MECO Vapor Compression Distiller Design
MECO’s evaporator is a vertical tube natural circulation design. The vertical arrangement allows the feedwater to be on the inside of the tubes, yielding numerous benefits to operation and maintenance. Feedwater boiling on the inside of the tubes allows that flow to travel up the tube and return to the base of the evaporator. This type of system is called a natural circulation evaporator design.
The VC systems that employ a horizontal tube evaporator design must force circulation using pumps and spray nozzles, increasing operating and maintenance costs. Feedwater should be adequately pretreated, with either dechlorination, reverse osmosis deionization, or softening to prevent scaling and corrosion in any evaporative type system. However, upsets in pretreatment can occur, and when they do, the benefits of NCE with feedwater on the ID of the tubes become obvious:
- No spray nozzles: There are no spray nozzles to become clogged. As a result, the scale is removed with cleaning solutions uniformly throughout the tube’s surface.
- No blocks: The clearance for fouling on the tube’s inner diameter is substantially greater than the clearance for fouling between the outer surface of the tubes in a horizontal bundle. Natural circulation vertical design won’t operate to the point where scale blocks the ID of the evaporator tube.
- No chemical damage: Spray systems typically deposit scales in isolated areas, exposing other tube bundle areas. Subsequent chemical cleanings will attack the bare metal while removing isolated scale deposits. Foulants within the feedwater in the tube can be brushed out from a vertical tube evaporator. In contrast, it’s physically impossible to mechanically clean foulants from outside a tube within a horizontal tube bundle.
- Efficient space: The vertical design provides a much more efficient use of space, minimizing the system’s overall footprint. Valves and instrumentation are easily accessible with a normal working height.
Tube Sheets
The evaporative section of the VC Still, commonly referred to as the Colandrea, contains the tube bank downcomer, steam chest, bent, and distillate box. The feedwater boils up the ID of the tubes, turning them into vapor. The water that doesn’t evaporate returns to the downcomer. All MECO VC Stills use a straight tube design requiring two tube sheets with the tubes rolled and expanded at both ends. It is more costly, but there are several benefits:
- Easily replace tubes without disturbing adjacent tubes or scrapping the entire bundle.
- This design allows MECO to provide an exterior finish of 25 ra or better on the surface area in contact with the distillate.
- The use of two tube sheets fixes the bundle at both ends, eliminating the need for baffling in a single U-tube bundle design. Baffling can cause crevices, surface scratches and corrosion problems.
- The straight tube design eliminates the need to bend the tubes, which is inherent in a U-tube design. In the absence of heat treatment, bending the tubes imparts residual stresses, which makes the bundle more susceptible to corrosion and disrupts the surface finish at the bends.
Feedwater Decarbonator
Stainless steels are susceptible to stress corrosion cracking, and several factors can influence an evaporator’s susceptibility. These factors are typically a function of the operating environment, such as the water quality, operating temperature, and construction materials and techniques.
MECO’s process in the evaporator considers the operating environment’s effects. Specifically, MECO’s Stills have a deaerator in the feedwater stream to remove oxygen, carbon dioxide, and other non-condensable gases before their harmful effects can have a chance to impact the evaporator.
WFI Generation System Using Vapor Compression
Let’s walk through the WFI generation process with a VC Still:
- The feedwater enters the unit and splits between feeding the distillate cooler and the blowdown cooler.
- These two heat exchangers preheat the feedwater while cooling the WFI distillate and blowdown from the evaporator.
- The feedwater then recombines and flows into the feed heater.
- Plant steam is introduced to the feed heater to further heat the feedwater to the proper temperature before it enters the decarbonator.
- The decarbonator removes CO2, O2, and other non-condensable gases before entering the evaporator. This helps reduce corrosion in the unit and results in lower conductivity in the WFI products.
- From there, the feedwater exits the decarbonator and travels to the bottom of the evaporator. The bottom head of the evaporator is a steam coil, which heats the feedwater during initial startup. It also keeps the unit at a self-sanitizing temperature — called hot standby mode. When the Still is not generating WFI, the steam coil allows for almost instantaneous WFI production when the downstream storage tank calls for water.
- From here, the feedwater boils up inside the evaporator tube’s generated vapors, which are then directed through our separator. The water that does not change to steam recirculates back to the bottom of the evaporator head through a downcomer.
- Then, some of that return is reboiled, and some is removed to the blowdown. The compressor draws the pure steam from there. The energy imparted results in compressed steam at an increased pressure and temperature.
- Higher energy steam is then discharged back into the evaporator on the outside of those evaporator tubes. That is where the steam condenses and gives up its latent heat, which is transferred through the tube wall to the feedwater inside the tubes.
- The pure vapor condensate on the outside of the tubes collects at the bottom and is withdrawn by the distillate pump. It gets discharged through one or more heat exchangers.
- Then, an in-line conductivity meter monitors the distilled water quality and directs the water to a WFI storage tank or to drain as waste.
MECO’s GII Centurbo™ Compressor
MECO has been in the biopharmaceutical market for over 40 years. During that time, we’ve supplied multiple vapor compression distillers to many pharmaceutical plants in the industry. The conventional technologies of those compressors were typically a dedicated compressor assembly that was then connected to either a belt system or a coupling back to a dedicated energy source. We were able to eliminate many of the mechanical components that would lead to wear or replacement.
Our GII Centurbo™ compressor uses a high energy density approach. It’s liquid cooled, so there’s no heat that needs to be ejected from the electrical portion of the motor. All of that is absorbed through a dedicated cooling system. The bearings are also supplied with an air-stream to help cool them.
Since the GII Centurbo™ is high energy, its weight and mass are quite small compared to equivalent motors of the same horsepower rating. The bearings systems are typically rated for over 6 years of service life in the field.
The GII Centurbo™ uses an air oil system for lubrication — top of the line technology when it comes to lubrication systems for bearings. The oil that’s delivered to the bearings goes into a waste cup — there’s no filtration or cooling system needed for that oil. The reservoir that holds that oil can last up to six months of operating time. Since the oil isn’t sprayed at a high velocity, there’s no risks for oil entrainment into air leaving the unit. No recirculation pumps or spray nozzles, no filters, no heat exchanger and pumping system to maintain.
One of the biggest advantages of the GII Compressor is how it is controlled by a VFD, so the compressor itself is variable speed.
Best Vapor Compression System for WFI
MECO’s VC Still delivers the best in industry innovation and performance. Elevate your vapor compression distillation for WFI with these advantages:
1. Ease of Access
As with all MECO products, our vapor compression system is designed to be as easily accessible as possible. The GII compressor placement allows for easy replacement. The distillate pump and air/oil system are easily accessed from the edge of the skid. They aren’t wedged between other components, ensuring easy access.
2. Quieter Operation
Eliminating belts and other mechanical components means MECO’s GII Compressor is extremely quiet. Operation sits at 72 to 85 decibels, below the OSHA requirement for hearing protection. Personnel in the water room do not need hearing protection, creating a more comfortable work environment. From a facility perspective, this gives operations the freedom to place office personnel closer to the water room without installing large noise abatement measures.
3. Compressor Removal
The compressor location makes it easy to access and remove as needed. The GII can be completely replaced within two hours, ensuring minimal service disruption. Additionally, the compressor is integrally mounted, eliminating the need for excessive ductwork and gasketing.
4. Fast Startup Hot Standby
MECO’s vertical tube VC evaporators use a heating coil inside the evaporator and an advanced control system to deliver rapid heat-up and hot standby operation. From a cold condition, MECO plants can come online in 45 minutes. Additionally, they’re instantaneously and reliably started from a hot standby condition. MECO also offers plate heat exchangers instead of heating coils. Plate heat exchangers provide lower utility costs and an increased heat exchange rate.
5. Advanced Automation Controls
MECO VC controls are still customizable for customers. We can accommodate custom tags for the programmable logic controllers. Additionally, MECO VC plants are fully automated and self-diagnostic. Our control system is also 21 CFR Part 11 compliant. The systems can be configured to cooperate with each facility’s data collection system.
6. MECO smartANALYTICSTM
MECO now has access to maintenance data generated by the Still. With this data, we can profile equipment operation. Get access to predictive maintenance with proactive scheduling based on Still data. Additionally, this technology lets users optimize operations and maximize cost savings — early issue identification avoids downtime and expensive repairs.
Advanced WFI Solutions From MECO
MECO’s vapor compression distiller is designed with energy efficiency in mind, and our VC plants are the most energy-efficient in the industry. MECO’s large surface area evaporators use less electrical power, translating to the lowest cost per thousand gallons produced. Additionally, our VC retrofit service offers control system upgrades and refurbishments to extend the life spans of distillers and water treatment systems.
With MECO on-site services, customers get installation services, startup support, preventive maintenance contracts, and more. Contact MECO today to explore our custom WFI generation system solutions!
MECO Webinar An Essential Review of Vapor Compression Technology for WFI Production from MECO Marketing on Vimeo.