Common Applications for WFI in the Biopharmaceutical Industry
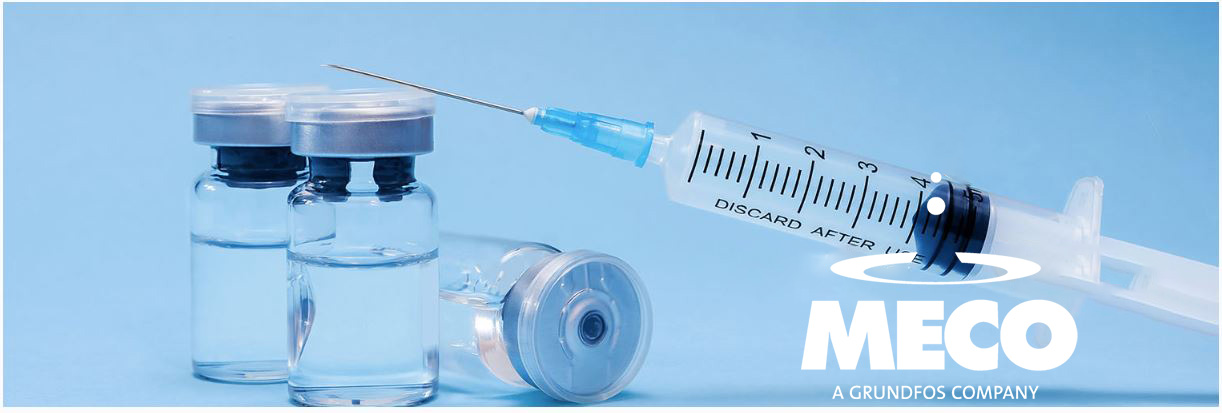
Water is a critical component in the biopharmaceutical industry as it is used in every stage of research, development, and manufacturing of products. However, the water utilized in these products is not typical tap water. Instead, different production methods are used for creating various types of water, such as Water for Injection (WFI). The production of WFI is an effective way to meet the demand for water use in the biopharmaceutical industry. MECO specializes in the production of pharmaceutical-grade water, delivering over 25 million gallons daily through highly engineered processes. In this article, we will cover what Water for Injection is, its uses, how it differs from purified water, and how it is produced.
What Is Water for Injection (WFI)?
Water for Injection (WFI) is a solvent that’s commonly used to dilute medications or solutions that are meant for injection into the body. In order to comply with regulations, WFI must contain very few chemical or biological agents that could potentially encourage the growth of microorganisms or bacteria. WFI systems typically utilize high-temperature environments and continuously-circulating water systems, which help to impede microbial growth in the water.
What Is Water for Injection Used For?
Water for Injection (WFI) is a highly purified form of water used in the pharmaceutical industry for various applications. Some of its key uses include:
1. Production of implantable medical devices: Biomedical manufacturers use WFI to ensure sterility in the production of implantable medical devices.
2. Hemofiltration: WFI plays a crucial role in filtering waste products from the blood and injecting sterile replacement fluids.
3. Cleaning laboratory equipment: WFI is important for maintaining sterile equipment and preserving the quality of products. It is used to clean containers and process equipment used in preparing parenteral drugs.
4. Diluting medicinal products: WFI is a sterile diluent for parenteral drugs due to its high level of purification.
5. Making parenteral drugs: WFI meets strict purification standards for drugs that are directly injected into the human body. Parenteral drugs include medication injected via the skin, veins, muscles, spinal canal, and heart.
Other uses for WFI include:
- Cleaning agents
- Eye health products
- Inhalation medications
- Cell culture growth media
- Rinsing bioreactors in biological therapies
- Fluid replenisher following a proper solute
WFI’s purified nature makes it ideal for cleansing anything that comes into contact with a drug, such as caps, vials, ampules, stoppers, and equipment used to store and process pharmaceuticals.
How WFI Is Produced
The production of WFI requires meticulous and complex processes. Three common methods are membrane-based systems, multiple-effect distillation, and vapor compression distillation.
Membrane-Based Systems
There are various methods of producing WFI, each with different costs of ownership. One approach is to use a membrane-based system such as reverse osmosis combined with ultrafiltration. Such systems are more cost-effective and take up less space. However, they require more monitoring and have a higher risk of contamination, although occasional hot water sanitization can reduce this risk.
To purify the water, a softener can remove hardness, and a carbon filter can remove chlorine. Reverse osmosis eliminates most of the dissolved ions, particulates, and organics. Electrodeionization can remove any remaining dissolved ions. Finally, ultrafiltration removes any endotoxins and bioburden that may still be present in the water.
Multiple Effect Distillation
Multiple effect distillers produce WFI using multiple stages of “effects.” In design, pharmaceutical multiple effect stills are modular and include options for exclusive and simultaneous pure steam production. Standard features include:
- Dual condensers
- PLC-based controls
- Hot standby option
- Vertical natural circulation evaporators
- Straight annealed tubes in the evaporator
- PID loop control of first effect pressure and feed water level
The unit is also assembled, wired, and piped on skids at the factory. Multiple effect distillation is the most energy-intensive method of producing WFI.
Vapor Compression Distillation
Vapor compression distillation is considered the most reliable method for producing WFI. The VC process for pharmaceutical distillation, typically begins with softened and dechlorinated water (at a minimum) and is boiled inside a bank of tubes. The generated vapor then passes through a mist separator to remove any impurities within the vapor generated from the feedwater supply. The pure vapor enters the compressor at controlled saturation pressure (and consequently temperature), where compression takes place, resulting in a higher saturation pressure. The higher-pressure (and temperature) compressed steam is discharged into the evaporator onto the outside of the tubes, where it condenses and gives up its latent heat energy to the boiling water inside the tubes. The VC process is very efficient thermodynamically since only about 10-15 BTU (11-16 kJ) of compressor work is used to recycle approximately 1000 BTU (1056 kJ) of the latent heat contained in the released vapors. Additional vapor is generated, and the process continues. The vapor, which condenses on the outside of the tubes, is collected and drawn off by the distillate pump and pumped through a heat exchanger. The excess feed water (blow down) is pumped through a heat exchanger. The distillate and blow-down are cooled in the respective heat exchangers while simultaneously preheating the incoming
feedwater. The heat exchangers help to minimize the energy consumption of the system.
The VC process has a relatively high economy as compared to the ME process. In addition, the feed water pretreatment requirements for a VC plant are typically less than that of ME plants. As such, in some cases where feed water pretreatment can be simplified, the overall capital investment for a VC-based system may be lower, and the operating costs are lower for the water purification process that employs VC. Overall system water recovery rates are sometimes higher for a VC application considering more efficient feed water pretreatment schemes and lower cooling water requirements.
Vapor Compression stills have the ability to produce water at both hot temperatures and ambient temperatures above the feed water temperature. The distiller can be switched between producing water at ambient temperature and hot water by opening and closing the valve around the distillate heat exchangers. One of the major advantages of an ambient (cold) VC Still is that it can periodically sanitize the storage and distribution system with hot water from the distiller. This type of still also recovers more heat and requires less plant steam to operate than one that produces WFI hot.
Some features of vapor compression include:
- Waste reduction
- Increased energy and water savings
- Variable production
- Simplified water pretreatment
- The ability to function at different temperatures
Another advantage of VC distillation is that if there is a leak in the evaporator, it will be detected during startup due to high conductivity. This is because the distilled water is processed at a higher pressure than the feed water, so any leakage occurs from the distilled water side of the heat transfer surface to the feed water side. In a membrane-based system, the feed water is always at a higher pressure than the product water. Therefore, if there is a loss of integrity in any of the membrane systems or the EDI, the water quality will be affected negatively. In the past, vapor compression systems have been criticized for their compressors, which are mechanical components necessary for proper operation. However, with modern advancements and diagnostics, these compressors have become highly reliable, and maintenance can often be completed in just a couple of hours if required.
Water for Injection vs. Purified Water
WFI and Purified Water are categorized based on their microbiological, chemical, and physical properties. Usually, a Purified Water system has two stages to treat feed water. These stages are pretreatment and final treatment.
The initial pretreatment stage modifies the water quality to eliminate or reduce metals, hardness, suspended solids, organics, scaling of downstream components, disinfectants, and any other harmful substances in the downstream unit operations. The second stage involves a modern system that pretreats water entering reverse osmosis membranes before passing through a deionization process or Electrodeionization (EDI) module. This further polishes the water, lowering its conductivity.
A Purified Water system may also include distillation. Vapor Compression is the most common method used to generate ambient water without an external cooling medium. Purified Water can be used in non-parenteral preparation for pharmacology applications, such as analyses and tests. It can also be utilized to clean equipment, as a diluent for non-sterile products, and as a pretreatment for the preparation of WFI. However, Purified Water is not adequately sterilized for use in sterile pharmaceutical products.
WFI is similar to Purified Water, as they are required to meet the same quality requirements. However, WFI must undergo additional treatment to adhere to strict endotoxin limits to be safe for injection. Systems that produce WFI must also undergo a validation process that ensures the water it is producing meets the required specifications. For WFI, the only three acceptable production methods are membrane-based systems, multiple-effect distillation, and vapor compression distillation. WFI is the purest regulated water product in this industry.
Partner with MECO
In biopharmaceutical manufacturing, Water for Injection is a critical component. There are several production methods that can be used, depending on various factors such as capacity, infrastructure, risk, reliability, energy efficiency, and water recovery requirements for each facility. Each system has its own advantages and disadvantages, and MECO can assist in determining the most suitable option for your WFI system.
For over 90 years, MECO has specialized in designing, constructing, and servicing engineered products and systems for Water for Injection, Purified Water, Ultrapure Water, and Pure Steam generation. As a world leader in the design and manufacture of water purification systems, our advanced technology and extensive experience enable us to offer valuable and sustainable solutions for our clients. We are committed to providing quality and innovative solutions to meet the world’s need for clean, pure water. Contact our MECO team to learn more.