A Cost Review of Four System Designs for Water for Injection (WFI)
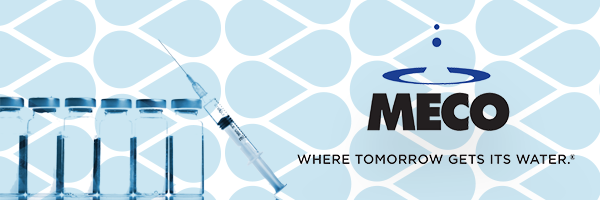
A Look at the Cost of Alternative Systems for Producing Water for Injection (WFI) Including Membrane-Based WFI Production Absent Distillation
In 2016, the European Pharmacopeia (Ph. Eur.) revised its monograph to allow “distillation or a purification process that is equivalent or superior to distillation in the removal of chemicals and microorganisms.” This new standard allows for WFI production via membrane, or ambient processes, such as reverse osmosis and other appropriate technologies.
Take a deep dive into MECO’s analysis of four different system designs and see how the cost of membrane-based systems compares to thermal technologies in the paper below.
Don’t want to scroll? Get your downloadable copy by filling out the form below.
Download a Cost Review of WFI Systems
Cost Review of WFI Systems
Water is a substantial ingredient in the drug manufacturing process. It is considered a critical utility and is produced in several bulk classifications. Purified Water (PW) and Water for Injection (WFI) are two of those classifications described in detail within various Pharmacopeia, including the United States (US), European, Japanese and Chinese Pharmacopeias.
Various methods of water purification are available to stakeholders in the drug manufacturing process. Each method has its own attributes related to quality, the total cost of operation, reliability, risk and sustainability. The US Pharmacopeia allows the production of WFI by distillation or means that are equivalent or superior to distillation. Until recently, the European Pharmacopeia (Ph. Eur.) required the use of distillation. Historically, distillation has been used for the production of WFI. In 2016, the Ph. Eur. revised its monograph to allow a “purification process equivalent to distillation such as reverse osmosis, coupled with
appropriate techniques.”
There was much discussion and debate prior to the Ph. Eur. decision to revise its monograph. The revision provides harmonization between the European and US Pharmacopeia, since neither now dictates a specific method of production. Ideally, there will be more opportunity for innovation in the development of alternative techniques for Water for Injection generation. The perceived risk associated with the elimination of distillation was one point of contention put forward by the European Medicines Agency. 1 In addition to harmonization, motivations also include sustainability and a reduction of total cost. 2 Subsequent to the issues raised by the EMA in March of 2008, a response was published in early 2009. 3 Among other issues, the response was critical of distillation and its ability to handle certain feed waters, high heat inputs and metallic compounds in the product water. Subsequent to the European Pharmacopeia monograph revision, the EMA published Questions and Answers on the Production of Water for Injection by Nondistillation Methods — Reverse Osmosis and Biofilms Control Strategies. Again, the EMA shared the main concern related to microbiological quality of the water produced and control mechanisms in place to minimize risk. 4
The assertion that there are cost savings to be realized by producing WFI via a membrane process has not been substantiated. It may seem intuitive that a distillation-based system costs more to operate than one reliant on membranes absent distillation, especially if the distillation system is normally preceded by a membrane-based pretreatment system. However, this is not necessarily the case. There are two different distillation methods commonly used in WFI production, multiple effect and vapor compression. There are a number of different membrane-based approaches to WFI production. Each of these methods has different costs of ownership.
The following is a brief cost analysis of four different but common system designs for the production of WFI. Although risk, reliability and sustainability are important factors in the evaluation of a systems cost, for the sake of simplicity and brevity, they are not considered in the scope of what is to follow. The analysis of total cost includes the first cost of capital, the operating utilities, including steam, electricity, feed water, cooling water and wastewater. Replacement parts, consumables and labor are also included.
View Our Pharmaceutical Solutions
Vapor-compression-based WFI production has a total cost of ownership that is less than or equivalent to that of a membrane-based system and significantly less than that of a typical multiple-effect-based system. The following examples illustrate system designs that are relatively basic, yet typically sufficient. The designs depicted yield a capital cost savings of 15%–28% for a membrane-based system relative to a distillation system. However, the operating costs are 35% greater than that of a VC-based system.
The four system designs under review are commonly used for the production of WFI. Each is rated at 1,500 liters per hour. The first system (System 1) uses multiple effect distillation with reverse osmosis as pretreatment. The second (System 2) is a membrane-based system
using reverse osmosis followed by electrodeionization and ultrafiltration. The third system (System 3) is a vapor compression distillation system. The fourth system (System 4) is a vapor compression distillation system with ultrafiltration as pretreatment. All of the systems utilize water softening and carbon filtration as a means of scale control and dechlorination of the feed water source. Each system design and operating parameters takes into account the same feed water supply quality.
The feed water supply in all examples has a hardness of 10 grains as CaCO3. The feed water hardness in conjunction with softener sizing dictates the frequency of softener regeneration with brine and the associated backwash and rinse cycles. The operating profile of each system is taken as 16 hours per day, seven days per week and 50 weeks per year. A chlorinated municipal feed water supply is assumed in each example, meeting drinking water standards. Each system under evaluation begins treatment with softening, although it is acknowledged that in many cases, there may be a need for additional particulate filtration. In any case, a specific feed water analysis will influence the ultimate system design. Product water recovery rates may be adjusted for any number of factors. The presence of chloramines, silica or other constituents within the feed water may dictate different configurations than what is presented here.
The capital, operating and maintenance costs associated with the foregoing systems and operating profiles are detailed within comparison Table 9 of all systems on page 17.
A detailed description of each system with associated capital and operating costs is as follows:
System 1 – Water Softening / Carbon Filtration / Reverse Osmosis (not hot water sanitizable) and Multiple Effect (ME) Distillation
System Description
Multiple effect distillation is the most commonly used method for the production of WFI throughout the world. The efficiency of a given distiller is defined by its economy (E) and dictated by the number of effects (columns) used in the design. Since the absolute value of the energy costs in an ME system can be significant, larger-capacity systems will typically have a greater number of effects to reduce the energy input to the system. Conversely, small-capacity systems may only have three to five effects, resulting in a lower capital cost. The system under evaluation here is rated at 1,500 L/hr. and has four effects, with a steam consumption of 561 kg/hr.
Given the elevated temperature of operation, multiple effect distillation normally has the feed water pretreated with reverse osmosis (RO) to remove dissolved ions that would otherwise promote scale or corrosion within the distiller. The RO unit effectively removes dissolved ions, bacteria, viruses and suspended solids. It is important to note that while the feed water quality is improved by RO, the improvement is not necessary to provide WFI quality of distillate from the ME, but only to protect the distiller from scale formation and corrosion. Scale formation will accumulate on the feed water side of the heat transfer surface, and its detrimental effect is to reduce the quantity of distillate produced, not the quality. As such, the quality of distillate is independent of the pretreatment. The phase change, separation system and temperature of the distiller effectively separate impurities and destroy microorganisms.
The RO unit will normally have water softening, carbon filtration and cartridge filtration as a minimum pretreatment for the removal of hardness, chlorine and particulate matter respectively. A single-pass RO unit, operating on an average municipal feed water supply, will have an energy consumption of 2.25 kilowatts and a product water recovery of 75%, with 25% continuously going to drain. The pretreatment system is not hot water sanitizable but has provisions for routine chemical cleaning. Given the operating pressures of both RO and ME, it is common practice to include an intermediate storage tank with a feed water pump. In this example, the pretreatment system and intermediate storage system are maintained through the use of chemical cleaning. A hot water sanitizable system could have been used but would have added to the capital and operating costs. The WFI product from the ME is produced and stored hot in a 4,000-liter tank, maintained hot at 80 deg C through the use of a trim heater and distributed out to the WFI loop.
Figure 1. A typical multiple effect distillation system with reverse osmosis pretreatment producing and storing hot (80 deg C) WFI. (System 1)
Capital, Operating and Maintenance Costs
Although specifications vary, the capital cost of the ME system described as a manufacturer’s standard can be budgeted at 673,900 € for reference in comparison to alternative systems being considered. The capital cost cited is Ex Works. It is exclusive of shipping and installation but includes commissioning, training and execution of IQ and OQ protocols. The total operating and maintenance costs for the system are estimated to be 177,957 € per year. Of the four systems considered, this represents the highest total cost of ownership.
The generation system as a whole has the following energy and water recovery profile:
1Feed rate is based on normal operation only. Does not include periodic backwashes or regenerations.
2This flowrate is only required during a regeneration step which occurs after a predetermined volume of water has passed through the softener. It is not included in the normal feed rate to the system.
3This flowrate is only required during a backwash/rinse step which occurs at a predetermined interval. It is not included in the normal feed rate to the system.
This system design is more attractive where the quantities of WFI required are small or intermittent, and the capital costs can be minimized by using a small distiller with a minimum number of effects (three–five). In this case, the absolute value of operating costs is less significant. This design is often considered a highly reliable approach considering the use of a membrane pretreatment system ahead of distillation. While this can be true to some extent, as noted previously, the water quality from the ME is relatively independent of the quality from the pretreatment. The membrane system’s primary role is to protect the ME system from scaling of the feed water surfaces and hence prevent downtime. Scaling of the distillation system heat transfer surface will diminish the capacity but not the product water quality. Another common misconception is that the same water is distilled many times over and hence ME distillation is inherently purer than other methods. It is easy to see the misunderstanding, since there are several columns and the units are referred to as “multiple effect.” In fact, each column distills a portion of the feed water only once, and that distillate is then cascaded in liquid phase through succeeding effects without further distillation and on to the condenser. The distillate from one ME unit is no more distilled or pure than that from any other ME or VC unit.
The maintenance schedule and replacement components are provided in tables 1 and 2 and are attributed to the cartridge filter and membrane replacement on the reverse osmosis pretreatment system as well as gasket replacements throughout the system and cleanings associated with disassembly and reassembly. The frequency of cartridge filter and membrane replacements will largely be a function of feed water quality and will be specific to each site installation.
Table 1. Basic maintenance schedule for RO/ME system. (System 1)
System 2 – Hot Water Sanitizable Reverse Osmosis / Electrodeionization/ Ultrafiltration/ Ultraviolet light / Ozonation
System Description
Distillation is not the only means by which WFI water quality can be achieved. Numerous system designs have been used utilizing reverse osmosis with the appropriate pretreatment, deionization and ultrafiltration. Variants to the core of the RO/EDI/UF design may include the use of ozone, ultraviolet light, double pass RO, a hot water loop and other components.
Table 2. Replacements for RO/ME system. (System 1)
The system under evaluation here utilizes softening, carbon filtration and cartridge filtration as pretreatment ahead of single-pass reverse osmosis, followed by electrodeionization and ultrafiltration. Similar to the previously described system, the softener serves to remove hardness and the carbon filter is for chlorine, while the RO removes dissolved ions, organics and particulate matter. Since the RO membranes do not remove 100% of the dissolved ions, the RO product water is fed to an electrodeionization system for polishing of the remaining ions. Ultrafiltration is used as a final polishing step to remove any organics that may remain in the system. The system is hot water sanitizable for the destruction of bacteria and equipped with provisions for chemical cleaning. The system under evaluation is rated at 1,500 L/hr. and consumes 9 kW in normal operation, excluding hot water sanitization, which consumes 90 kW. The product water recovery rate is 67.5%, considering backwashing and rinsing of the softeners and carbon vessel as well as reject from the RO and EDI. For this design, ozone is used in storage of the product water while ultraviolet light is used for ozone destruction. There are numerous variations and options that can be employed in the design of a membrane-based system, including chemical injection, membrane degassification, double pass RO and ceramic UF membranes, as well as hot water storage and distribution, among others. These options typically add to the capital cost of the system without reducing the ongoing operational cost.
As such, the basic system previously described represents an aggressive cost approach for comparative purposes. It should also be noted that on small systems such as that under discussion, the addition of instrumentation and valving for trend analysis, biomonitoring, intermediate sampling and other operational needs can substantially increase the cost of the system. In a conservative effort to evaluate differential capital cost, much of these options are excluded here. It is also acknowledged that the use of ozone may not be desirable, and in that case, the storage and distribution loop would employ heat exchangers for heating and cooling, with the associated capital and energy.
Figure 2. A basic membrane-based WFI production system using reverse osmosis, electrodeionization and ultrafiltration, with ozonation and UV destruct at ambient temperature. (System 2)
In contrast to a system design incorporating distillation, the WFI water quality in a membrane-based system such as this is not generated in one step utilizing a phase change. In a membrane-based system, the RO membranes, EDI unit and UF system each serve to remove a specific set of constituents from the water, and the effectiveness of each is directly dependent upon the feed water quality generated by the upstream component. It has been said that “It is the maintenance of the feed stream’s essential quality that is the key to the proper performance of the RO or distillation operation. Neither distillation or RO is the complete show.” While this may be true to some extent, comparatively, the distilled water quality is relatively independent of feed water quality, while the membrane-based system’s water quality is directly dependent on and influenced by the quality of the feed water to each unit operation. Within a membrane-based WFI generation system, each of the three main process components (RO/EDI/UF) is critical to achieving the final water quality. A failure in any one of the components will have an adverse impact on the water quality downstream. The normal operator intervention and maintenance associated with a membrane-based system will be higher than that of a distillation-based system. Particulate and biological fouling of cartridge filters and reverse osmosis membranes necessitate hot water sanitization, chemical cleaning and replacement of elements. The use of ultraviolet light for ozone destruct or within the generation system itself will require replacement of quartz sleeves and UV lamps. The frequency of replacements and sanitization of the system will influence the manpower and replacement cost of components. 5
Considering the interdependence of reverse osmosis, electrodeionization, ultrafiltration, ozonation and UV destruct on final water quality, the sampling and calibration requirements will be higher for a membrane-based approach.
View Our Pharmaceutical Solutions
Capital, Operating and Maintenance Costs
The capital cost of the membrane system described as a manufacturer’s standard can be taken as 513,480 € for reference, compared to alternative systems considered. The capital cost is Ex Works and exclusive of shipping and installation but includes commissioning and validation. While pricing from different manufacturers may vary, the costs for all of the systems here are from the same manufacturer in an attempt to provide relative cost differences that are comparatively accurate. In addition, the membrane-based system described in System 2 represents a fairly basic and standard design. It is acknowledged that there are many deviations to the basic design that could achieve the same water quality. However, these variants would add to the capital cost and increase complexity, with the associated impacts to operation.
The total operating and maintenance costs for the system are estimated to be 101,200 € per year. Of the four systems considered, the membrane-based system outlined here represents the lowest capital cost but the second-highest operating and maintenance costs.
The membrane-based system as described has the following energy and water recovery profile:
1Feed rate is based on normal operation only. Does not include periodic backwashes or regenerations.
2This flowrate is only required during a regeneration step which occurs after a predetermined volume of water has passed through the softener. It is not included in the normal feed rate to the system.
3This flowrate is only required during a backwash/rinse step which occurs at a predetermined interval. It is not included in the normal feed rate to the system.
The maintenance schedule and replacement items are provided within tables 3 & 4 and are largely attributable to the cartridge filter, membrane and EDI cell replacements as well as gasket replacements throughout the system and cleanings associated with disassembly and reassembly.
Table 3. Basic maintenance schedule for RO/EDI/UF system. (System 2)
Table 4. Replacements for RO/EDI/UF system. (System 2)
System 3 – Vapor Compression Distillation with Water Softening and Carbon Filtration as Pretreatment
System Description
Vapor compression (VC) is the most energy efficient means to distill water. Producing hot WFI (82 deg C), a multiple effect distiller will require eight–10 effects to compete with the energy consumption of a VC plant. 6 A significant advantage of the VC cycle that is not available in ME distillation is the heat recovery associated with the production of ambient temperature distillate. In this case, the efficiency of the VC cycle further improves, over 2.5 times that of hot WFI production. As such, distilled water can be produced at ambient temperature with a much higher efficiency. The distiller can be switched between the ambient mode and hot production through valve actuation around the recovery heat exchanger. The benefit of this operation is the ability to periodically sanitize the storage and distribution system with hot water from
the distiller. Another advantage of the VC cycle is that it typically has the ability to operate on a simplified pretreatment system without the need for reverse osmosis. VC plants operate at lower temperatures than ME units and are therefore less susceptible to scaling and corrosion. As such, many VC plants used in the production of WFI use only softening and carbon filtration as pretreatment.
In the ME system, a disruption in the feed water softening system will result in scaling on the feed water heat transfer surface and a loss of capacity, but this is not detrimental to the water quality. Chlorine will cause stress corrosion cracking of stainless steel at high temperatures, causing the distiller to leak first at areas of stress, such as welds or tube to tube sheet joints. Ammonia carry-over will present itself as high conductivity and is readily detectable. One benefit of VC distillation is that the distilled water is processed at a higher pressure than the feed water.
Figure 3. A typical vapor compression system producing distilled water at ambient temperature with periodic hot sanitization of the loop. (System 3)
As such, in normal operation, any leakage progresses from the distilled water side of the heat transfer surface to the feed water side as opposed to the other way around. A leak within any one of the exchangers will present itself as high conductivity on startup. In the membrane-based system previously described, the feed water is always at a higher pressure than the product water, and a loss of integrity in any one of the membrane systems or the EDI will adversely impact the product water quality. Vapor compression systems have historically been criticized over the compressor, a mechanical component necessary for the proper operation. Modern sanitary direct drive centrifugal devices with onboard diagnostics have made these compressors highly reliable. Maintenance of seals and bearings is often accomplished through a complete swap-out of the device in a matter of a few hours. 7
Capital, Operating and Maintenance Costs
The capital cost of the VC system described as a manufacturer’s standard can be taken as 608,700 € for reference in comparison to alternative systems considered. The capital cost is Ex Works and exclusive of shipping and installation but includes commissioning and validation. The total operating and maintenance costs for the system are estimated to be 75,100 € per year. Of the four systems considered, VC with water softening and carbon filtration has the lowest cost of ownership and the second-lowest capital costs (just behind the membrane-based system). The VC-based WFI generation system has the following energy and water recovery profile:
1Feed rate is based on normal operation only. Does not include periodic backwashes or regenerations.
2This flowrate is only required during a regeneration step which occurs after a predetermined volume of water has passed through the softener. It is not included in the normal feed rate to the system.
3This flowrate is only required during a backwash/rinse step which occurs at a predetermined interval. It is not included in the normal feed rate to the system.
The maintenance schedule and replacement items are provided within tables 5 and 6. The system benefits from the elimination of RO and the associated maintenance, filter and membrane replacement as well as an improved water recovery rate.
Table 5. Basic maintenance schedule for CF/WS/VC system. (System 3)
Table 6. Replacements for CF/WS/VC system. (System 3)
Figure 4. Ultrafiltration membranes ahead of vapor compression distillation provide removal of suspended solids and bacteria from the feed water supply without some burdens associated with reverse osmosis pretreatment. (System 4)
System 4 – Vapor Compression Distillation with Water Softening, Carbon Filtration and Ultrafiltration as Pretreatment
System Description
Distillation has been criticized as yielding log reductions of only 3.0–4.0 and hence feed water in excess of 300 eu/ml is susceptible to endotoxin carryover. Guidelines provide that distillation should yield a minimum log reduction of 3. 8 As such, an EPA drinking water supply to a distiller would have to be out of control within its pretreatment to generate such an endotoxin load. The bioburden load in the distillation systems described is controlled via steam sanitization of the pretreatment vessels. Despite the foregoing, a membrane barrier within the pretreatment system will reduce the bioburden on downstream processes. In this instance, ultrafiltration is a good application ahead of vapor compression with several benefits, while excluding the less than desirable aspects of RO membranes. The UF membranes remove suspended matter, bacteria and viruses while passing through dissolved solids. Dissolved solids have no impact on VC distillation, assuming the scale-forming constituents are removed in the upstream softener. The exception to this is when there are high silica levels in the feed water that can’t be managed by increasing the blowdown, which will require a silica removal step.
The term ultrafiltration is fairly generic and refers to a particle size removal capability. So, as not to avoid confused with cartridge-based or spiral wound ultrafilters, those used in advanced water pretreatment systems under discussion here can be characterized as constructed with polymeric material in a hollow fiber configuration. Further, the UF membranes under discussion offer the following characteristics.
1. UF membranes are chlorine tolerant, while RO membranes are not.
2. UF membranes are backwashed and rinsed, while RO membranes are not.
3. UF membranes are more robust and have a significantly longer life than RO membranes.
4. A typical UF system operating on city water will recover more than 90% of the feed water.
Capital, Operating and Maintenance Costs
The capital cost of the UF/VC system described as a manufacturer’s standard can be taken as 720,000 € for reference in comparison to alternative systems considered. The capital cost is Ex Works and exclusive of shipping and installation but includes commissioning, training and validation.
The total operating and maintenance costs for the system are estimated to be 89,700 €. Of the four systems considered, the UF/VC system represents the second-most-expensive capital expenditure behind the RO/ME system but offers significant operating advantages relative to the membrane-based system and the ME system. The UF/VC-based WFI generation system has the following energy and water recovery profile:
1Feed rate is based on normal operation only. Does not include periodic backwashes or regenerations.
2This flowrate is only required during a regeneration step which occurs after a predetermined volume of water has passed through the softener. It is not included in the normal feed rate to the system.
3This flowrate is only required during a backwash/rinse step which occurs at a predetermined interval. It is not included in the normal feed rate to the system.
The maintenance schedule and replacement items are provided within tables 7 and 8. The system benefits from the “belt and suspenders” approach of a membrane-based pretreatment system without the level of maintenance required for RO.
Table 7. Basic maintenance schedule for VC/UF system. (System 4)
Table 8. Replacements for VC/UF system. (System 4)
Summary
Although there have been assertions that a membrane-based system offers a lower cost of WFI production, this is not necessarily the case. The foregoing analysis indicates that while a membrane-based system offers capital and operating cost advantages over a multiple-effect-based system, the same is not necessarily true for a VC-based system. The VC-based systems have a lower operating cost than both the membrane-based system and the multiple-effect-based system.
In its simplest form, a membrane-based WFI system offers the advantages of a low capital cost and low energy consumption. As previously mentioned, the simplest design is not always what is required. Double pass RO, hot water storage, degasification, biomonitoring and other features may be specified on a membrane-based system and in this case, the capital cost advantage may become negligible or eliminated entirely in comparison to a VC-based system (Systems 3 & 4). Over time, the membrane-based system has a higher overall cost than a VC-based system (System 3) given the higher cost of replacements and manpower. It is also noted that the membrane-based system has the highest total budgeted downtime hours (714) for maintenance, sanitization and replacement items. No cost has been attributed to downtime given a system utilization of only 5,600 hours/ year.
The lowest total cost of ownership is the VC-based system pretreated by softening and carbon filtered water. The VC-based system has a significant energy advantage over ME producing WFI at ambient temperature through heat recovery that is not available in a ME-based system. The VC-based system also benefits from a simplified pretreatment system that does not require RO Elimination of reverse osmosis in pretreatment also contributes to lower downtime hours and hence more online availability. The overall water recovery is highest in the VC-based systems. While the capital costs of the VC-based systems are slightly more than a membrane-based system, the operating costs are as much as 25% lower. Although the VC system is producing ambient temperature WFI through a heat recovery heat exchanger, it has the benefit of being continuously distilled with periodic heat sanitization of the storage and distribution system.
The VC-based system using ultrafiltration for pretreatment provides the benefit of a membrane barrier for added microbial control within the system without the replacement, maintenance and downtime associated with RO membranes.
Table 9. WFI Production System Comparison