Digitalization in the Pharmaceutical Industry
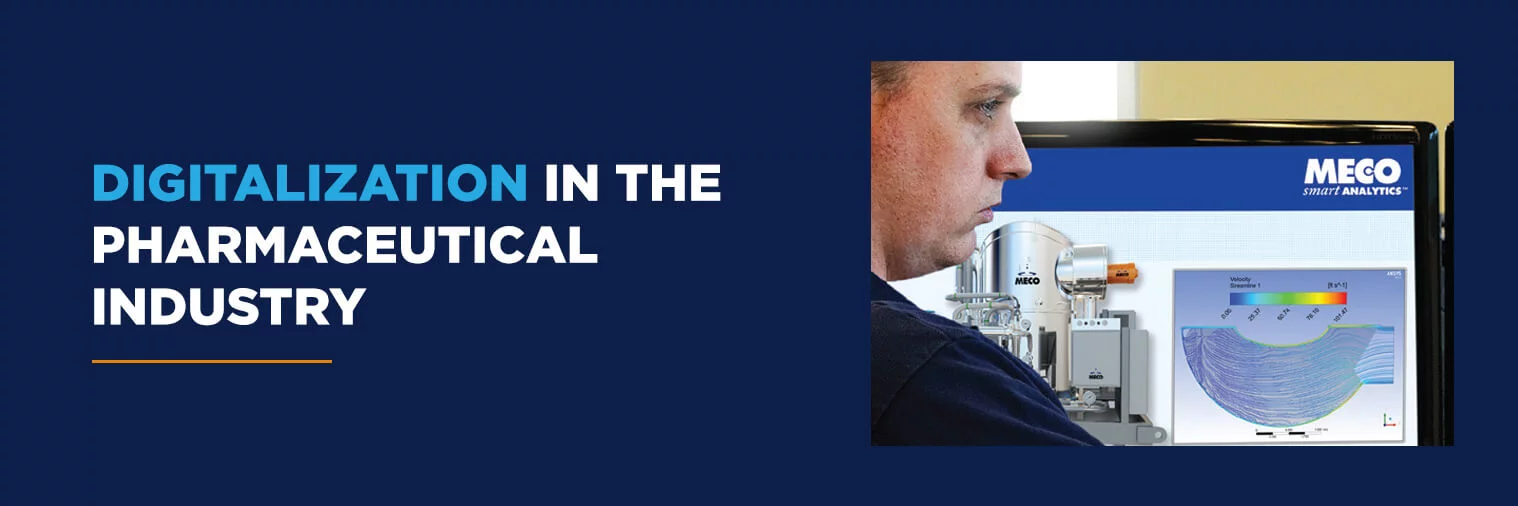
The COVID-19 pandemic created a significant increase in digitalization since 2020 due to nationwide lockdowns and social distancing requirements. Studies show this global health phenomenon resulted in a 6-year digital transformation acceleration, with 97% of business executives stating that the pandemic expedited their digitalization efforts.
Recent surges in digital transformation have played a major role in enhancing corporate strategies across all industries, enabling companies to elevate their operations and produce better business outcomes. Despite this recent spike, the pharmaceutical industry has resisted adopting digital tools and changing its strategic priorities and workplace culture due to complex manufacturing processes. Still, the growing demand for drugs emphasizes a clear need for pharmaceutical digitalization.
What Is Digitalization in the Pharmaceutical Industry?
Digitalization in the pharmaceutical industry is the process of integrating digital technologies across all areas of a business to improve operations and deliver greater value to customers.
Pharmaceutical digitalization involves developing and incorporating digital technologies across all levels of business operations. Through this process, industry professionals collect, analyze, and use high volumes of data from various sources to support objectives like:
- Drug manufacturing.
- Research and development.
- Supply chain management.
- Clinical development.
- Patient engagement.
- Quality assurance and control.
How Is Digitalization Improving the Pharmaceutical Manufacturing Industry?
Digital transformation offers many growth opportunities for the pharmaceutical industry, delivering significant process advantages that eliminate siloed systems and long-standing manufacturing inefficiencies. As a result, pharma companies can better meet future demands.
Digitalization is affecting the pharmaceutical industry and its manufacturing processes in many ways.
Increased Visibility
Digital technologies enable companies to make more informed business decisions by increasing their supply chain operations visibility. With digitalization, organizations can fully integrate their supply chains to improve manufacturing processes through more responsive and adaptive operations. These changes result in greater accuracy, inventory levels, manufacturing efficiency, and service, allowing businesses to make faster and more effective business decisions.
Digitalization also delivers greater visibility across value chains for pharmaceutical manufacturers. This increased data visibility leads to valuable insights that these businesses can use to learn from their existing processes and improve their drug designs.
Cost Reductions
Digital transformation helps to lower per-capita costs in the pharma industry. In manufacturing plants, digitalization often involves machine learning, artificial intelligence, and machine-to-machine communication. These digitalized processes promote seamless manufacturing operations, automated corrective actions, and better preventive maintenance. As a result, pharmaceutical companies experience fewer errors and malfunctions. By preventing equipment breakdowns, digitalization minimizes repair expenses, liabilities, and downtime, leading to greater cost savings.
Improved Efficiency
Forty percent of executives listed operational efficiency as a top benefit of digital transformation. Pharmaceutical companies can increase their manufacturing efficiency and productivity through digital transformation. Digitalization allows businesses to collect data across their entire facilities, giving decision-makers key insights into their companies’ overall operational efficiency. They can also analyze these insights to pinpoint process inefficiencies and determine how to improve these areas.
In addition to increasing efficiency through insight analysis and implementation, digitalization also enables pharma companies to automate various aspects of their manufacturing processes. That means they can achieve more work in less time while using fewer resources and manual labor.
Greater Flexibility
Digital transformation in the pharma industry allows for more flexible manufacturing processes, improving medication and vaccine production speeds when compared to traditional fixed processes. Unlike fixed production processes, flexible manufacturing lets companies produce new drugs in facilities that use single-use materials, allowing them to bypass equipment cleaning validation for current machines. This adaptability saves companies manufacturing time, enabling them to send drugs and vaccines to market for customers faster.
Digitalization in the pharmaceutical industry also allows for flexible manufacturing equipment. Companies can adjust these machines to accommodate changing patient demands while improving patient safety through robotics and automation. Flexible manufacturing helps companies better achieve medication compliance.
Higher Product Quality
Pharmaceutical companies gather procedural data to ensure product quality. However, many of these organizations rely on paper documentation in their facilities, creating gaps in the quality assurance process. Studies show that it takes pharmaceutical companies a minimum of 6 months to onboard quality management staff because of the high number of systems and data sources they must use to do their jobs, along with a lack of real-time data access.
While paper documentation through manual spreadsheets and reports is time-consuming and prone to errors, data collection and management through digitalized technologies improve process efficiency and reduce the risk of mistakes. Digital transformation helps pharma companies collect information from numerous sources, standardize it, and analyze it to improve quality assurance. It also allows real-time monitoring across a plant’s processes and production levels to close quality gaps and improve reporting workflows.
All these digitalization capabilities enable pharmaceutical companies to improve quality control, reliability, and efficiency, resulting in higher-quality products.
Increased Control
When manufacturing pharmaceutical products, every process must be meticulously monitored, such as product development, equipment cleaning, and packaging labeling. That is because a single error in these processes can render an entire batch of products unusable, costing companies time, money, and resources. In addition, faulty batches can cause serious harm to consumers, resulting in lawsuits and reputational damage to companies.
Digitalization in the pharma industry helps organizations better control their manufacturing processes with greater product monitoring, visualization, and remote data access, allowing them to identify and improve packing processes. As a result, they can pinpoint and address errors before they impact product batches, leading to higher profitability and cost savings.
Competitive Advantages
Integrating digital technologies into pharmaceutical processes enables companies to improve manufacturing operations, reduce costs, and increase production quality. Because digitalization comes with these significant benefits, it offers businesses that embrace it a clear competitive advantage over pharmaceutical companies that have not digitalized their operations. By prioritizing digitalization in their supply chains, pharma companies can experience greater outcomes for their businesses that will set them apart from other organizations.
Leverage MECO smartANALYTICS™ for Digitalization in the Pharma Industry
Pharmaceutical companies can embrace digital transformation in their manufacturing facilities and improve water system performance with analysis services from MECO. Through MECO smartANALYTICS™, our expert engineers ensure that water systems operate with optimal performance while minimizing environmental impact, consumables consumption, and downtime. Our team evaluates, monitors, and reports on our customers’ system performance to optimize operational efficiency in the long term.